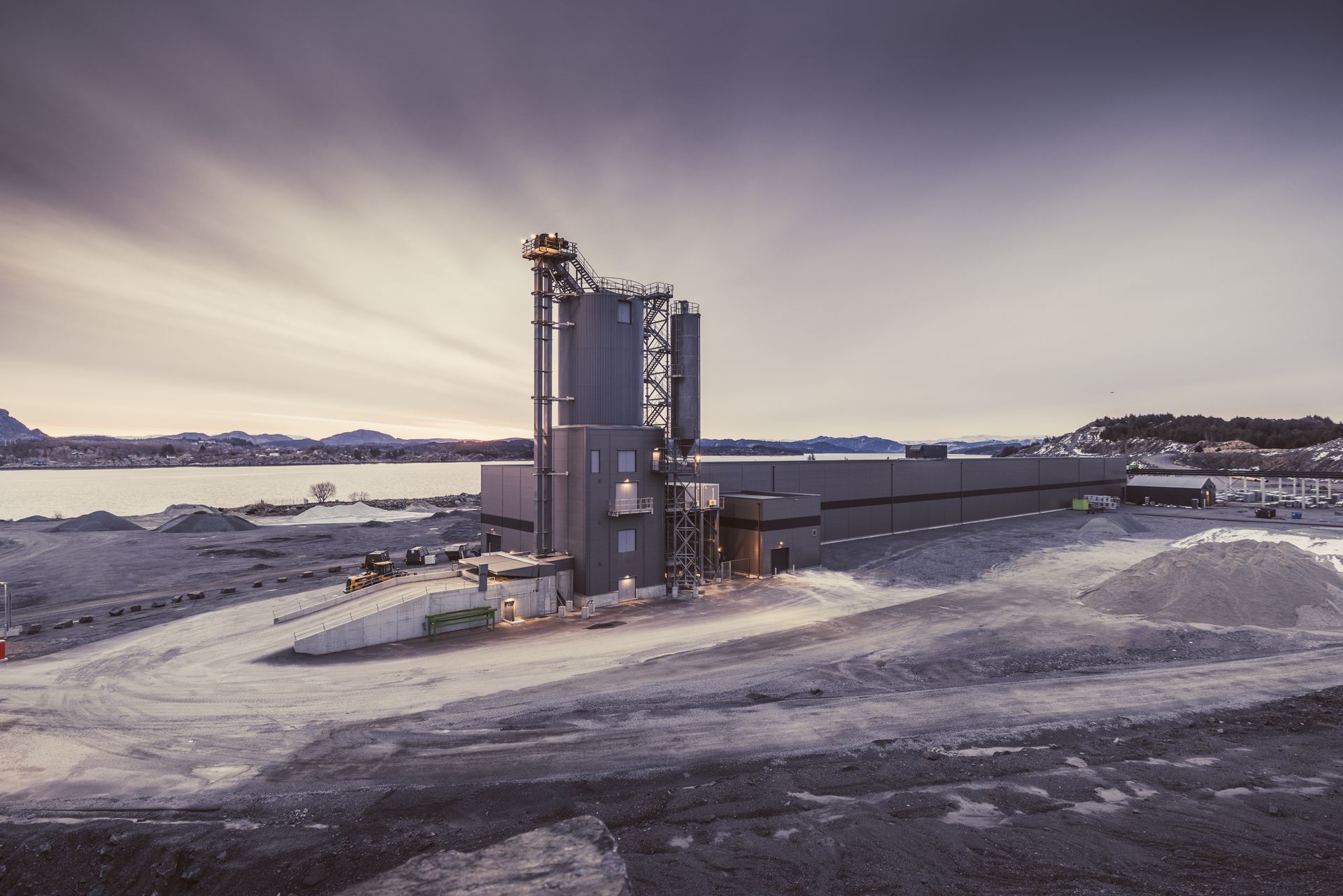
Next Level Automation in Hollowcore Production
On the island of Askøy, just off the western coast of Norway, a new and innovative hollowcore plant is up and running. Set up by Contiga, one of the country’s leading precast manufacturers, this ambitious project aimed to reduce labor costs through high levels of automation.
Contiga, part of HeidelbergCement, delivers prefabricated elements in steel and concrete. The company’s products include hollowcore, walls, stairs, beams, columns, and balconies. These can be found in projects all around Norway, from commercial buildings to apartment blocks, public buildings to sports arenas and elsewhere.
The new factory in Askøy has been operational since spring 2021, and only requires 10 operators to run 3 production beds daily.
Production Director, Hilde Fløgstad, explains:
“The layout of the factory is very good, and the speed of the machinery is impressive. I am proud of the level of automation that we have achieved. We can do a lot with quite limited resources.”
Fløgstad goes on to explain how this is important in Norway, where labor costs are high:
“That is the only way we can stay competitive in this market.”
Contiga partnered with IPHA Associate Members, Elematic, having worked with them before, and also being confident in their ability to deliver the automation required:
“It was one of the companies that had come furthest with regards to automation, and it had a wide range of products. When building a highly automated factory, you need the IT bit to be in line too.”
The production at Askøy is monitored and planned with Elematic Plant Control.
Flexible Operators
When Contiga Askøy started casting in 2021, it was with a completely new team of operators. As Contiga’s Technical Advisor Ove Sandvin explains, it didn’t take long to get up and running:
“At the moment we are operating in only one shift, and we are producing three beds a day. At the plant, we have four beds which are 132 meters each, which will give us a maximum capacity of 240 000 m2 per year.”
Thanks to the high level of automation, the plant only has 13 employees, with 10 operators working at a time during normal production (180,000 m2).
Having a smaller workforce reduces labor costs, but it can also leave production vulnerable to unforeseen absences. At Askøy, the operators rotate between different tasks every other week, ensuring flexibility in all aspects of production.
Innovative Projects
Amongst the major projects Contiga is involved with is the Barcode area in central Oslo, and the administrative headquarters of Vestland county in Bergen, in the area in which Askøy is located.
Fløgstad is particularly proud of an emergency ward project in Oslo:
“We delivered new elements, but we also reused elements from the government quarter in Oslo.”
The Norwegian government quarter was bombed during Anders Behring Breivik’s terrorist attack in 2011. Any surviving elements were recovered and cut before transportation to one of Contiga’s other factories, in Moss. After refurbishment, they were then given a new life in Oslo.
“It is a great project in terms of sustainability, and we are very happy that we succeeded,” she continues.
In fact, Fløgstad can see a future where new preast elements will be installed alongside used ones:
“We are working on how to make it easier. There is a Norwegian standard now that also gives guidelines on what can be reused and what requirements we have to fulfil.”
Optimal Factory Layout and Production Efficiency
Reuse of old elements isn’t the only way to recycle concrete. At Askøy, unused concrete is ground up and reused in the mix along with slurry from the recycling plant.
“To build a new factory without a recycling plant is very unthinkable these days. Recycling is just as important as the core processes in our production. We need to reduce our waste and leave a CO2 footprint that is as low as possible.”
The Askøy plant layout was designed for efficiency in production, but also in terms of maintenance, cleaning and transport.
Both Fløgstad and Sandvin highlight the batching & mixing plant, automated concrete delivery and multistressing systems, and automated lifting equipment for transporting finished slabs.
Sandvin goes on to explain:
“The Modifier E9 saves our personnel from the toughest jobs, and we save about 1.5 operators behind the machine.”
The speedy Extruder E9 is also worth mention, Sandvin notes:
“We have cast up to 2.8 meters per minute for a 265 slab. I think that is quite fast!”
Contiga AS are full members of IPHA, and work alongside associate members Elematic.
This case study was originally published on the Elematic website.
Title
Contiga AS – Elematic
Project Type
Hollowcore Production
Production Started
2021
Project Facts
- Production started 2021.
- Maximum production output: 240,000 sqm.
- 13 Operators (10 working at any time).
- Involving IPHA member – Contiga AS and Associate Member – Elematic.
- 4 x 132m production beds.
- Contiga AS employs 500 people at 11 locations in Norway.